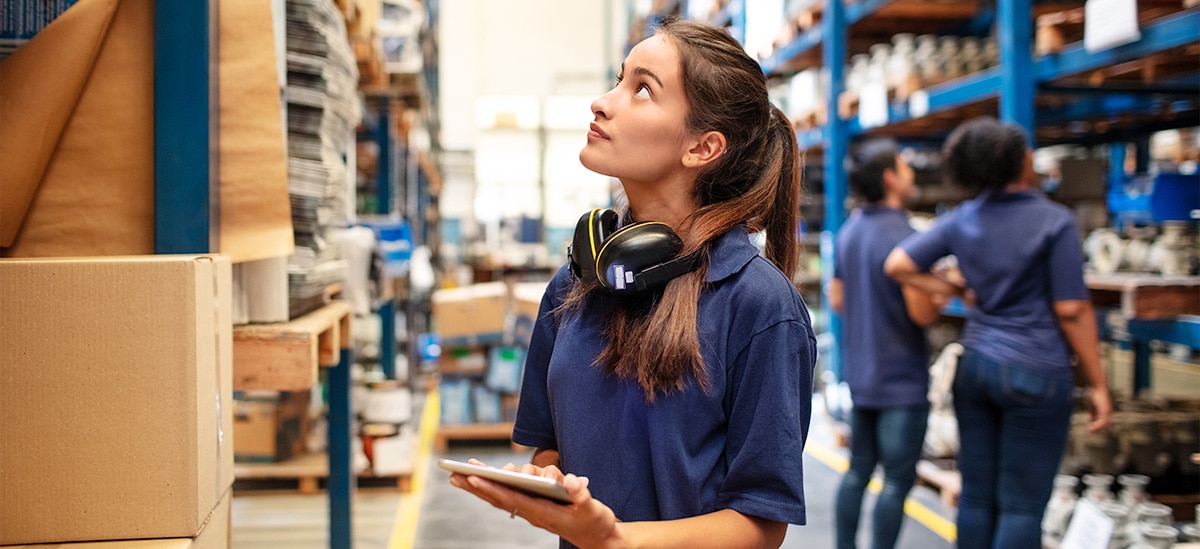
The manufacturing sector is primarily firing on all cylinders. The May 2024 Federal Reserve report finds industrial production running at nearly 80% capacity.[1] Yet that figure was down slightly from 2023 levels, illuminating the need for manufacturers to ensure continued progress by minimizing pain points and taking advantage of opportunities to grow.
Here are five potential challenges you may face with solutions that could help you fine-tune your approach and proactively adapt to fluctuating conditions.
Challenge 1: Ongoing Shortage of Skilled Labor
A McKinsey study notes that fewer Gen Z workers are entering the field than required to fill expected factory vacancies. This is an emerging threat given that there is an expected wave of retirements soon as nearly one-third of the manufacturing workforce was over 55 in 2022[2, 3]
Solution:
The good news is that Gen Z cites meaningful work as one of their top priorities, which allows manufacturers an opportunity to emphasize the path they provide to make a positive impact on society. When recruiting talent, consider highlighting how your product improves lives or the elements of your process that promote sustainability.
Working conditions matter, too. While manufacturing roles were once seen as static, with limited opportunities for advancement, the field now offers a dynamic and evolving career path due to the increased reliance on technology and opportunities to upskill and cross-train.
Another option to the staffing conundrum is to turn to technology to augment your workforce. “Cobots,” which labor alongside workers, automate routine tasks so that employees can focus on higher-level, more fulfilling tasks. One manufacturer found that cobots enhanced productivity by 40% and improved resource utilization by 50%.[4]
Challenge 2: Financing the Transition to Industry 4.0
The digital transformation of the manufacturing sector continues unabated, and although technological evolution is changing the game, the necessary upfront investment can be a barrier. The Smart Factories and Digital Production survey conducted by the National Association of Manufacturers (NAM) found that nearly 70% of survey respondents said their Manufacturing 4.0 investments this year would continue unchanged from last year, and nearly 19% said they would increase investment.[5]
Solution:
Pivoting to a smarter factory could future-proof operations and modernize the manufacturing process through related upgrades like automation, data analytics, and IoT systems, which can help improve productivity and reliability.
As you consider which systems are right for you, it’s important to be judicious about your upgrades. A Gartner study found that identifying the right technology (47%) and compatibility with their existing systems (44%) were cited by manufacturers as their biggest challenges when planning investments in new software.[6] In addition, make sure you have a solid plan for securing funding. That’s where short- and long-term financing, from lines of credit to loans, can help you get ahead.
Challenge 3: Cybersecurity Woes
While technological upgrades hold promise for improved output, an increased reliance on digital systems can also have a downside. With more equipment controlled by computers, there’s an escalating opportunity for hackers to launch a “denial of service” attack to shut down operations. According to Statista, manufacturing experienced the greatest percentage of cyberattacks among top industries globally in 2022.[7] And because most manufacturers operate on a “just-in-time” schedule, they can be particularly susceptible to becoming a victim of a ransomware attack.
Solution:
Consider maintaining good security “hygiene.” Conduct timely patching and regularly review security protocols to detect vulnerabilities. Manufacturers should also consider prioritizing backing up data and maintaining an updated incident response plan. Consider coupling that with robust, round-the-clock monitoring—whether from in-house talent or by outsourcing to a specialist—to identify threats.
While these activities and services can be expensive, the upfront cost of prevention is a small fraction of the alternative—giving in to hacker demands or suffering the effects of extended downtime.
Challenge 4: Continuing Supply Chain Disruption in Certain Segments
While many of the supply chain wrinkles have been recently ironed out, there are still lingering issues in targeted areas. For many brands, that includes a shortage of the chips that are used in a wide range of products, from consumer electronics to household appliances and medical devices.
Solution:
The shortage could begin to ease as the CHIPS Act (Creating Helpful Incentives to Produce Semiconductors for America) comes online. This legislation allocated $39 billion in domestic manufacturing incentives and $11 billion for chip research and development. And a report from the Semiconductor Industry Association (SIA) and the Boston Consulting Group found that chip-fabrication capacity will jump 203% from 2022 to 2032.[8, 9]
Even small blips could affect manufacturers due to the web of suppliers they typically use. Delays might lead to production halts and the need to warehouse materials that have already arrived while you wait until all components are available to resume. Greater visibility into the supply chain through AI, machine learning, and advanced analytics helps manufacturers avoid costly surprises and ensure production is ready when the materials arrive.
Challenge 5: Unplanned Downtime
When factories sit idle, manufacturers lose money. One report found that the cost per hour of downtime is soaring—with a lost hour ranging from $39,000 for factories producing consumer packaged goods up to $2 million for automotive companies.[10]
Solution:
One of the best ways to minimize unplanned downtime caused by machine error is through predictive analytics, which can forecast when a piece of equipment is likely to fail. As sensors installed on the equipment collect performance data, the analytics look for patterns in real time that might indicate an imminent problem, such as a change in temperature or vibration levels.
Once a potential issue is identified, the maintenance team can perform repairs proactively, reduce downtime, and increase productivity. As with other technological advancements, investing today might bring positive ROI for future operations.
Paving The Way for Progress
The manufacturing landscape continues to transform at lightning speed so companies need to stay agile to stay ahead. To find out more about PNC’s solutions for manufacturers, contact us today.